Essential Guide to Industrial Electronic Equipment Usage
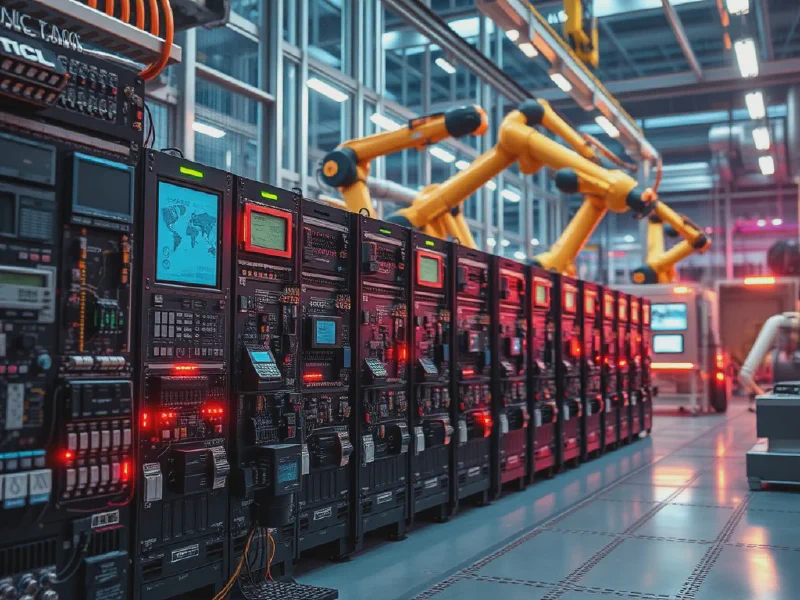
A Comprehensive Guide to Industrial Electronic Equipment
Industrial electronic equipment plays a crucial role in various manufacturing and production environments, facilitating automation, control, and monitoring processes. These devices range from simple sensors to complex control systems, contributing significantly to operational efficiency and safety in industrial applications.
Understanding the different types of industrial electronic equipment is essential for professionals involved in engineering, manufacturing, and maintenance. This equipment is designed to withstand harsh conditions typical of industrial settings, ensuring reliability and performance over extended periods of use. Key components include control systems, sensors, power supplies, and programmable logic controllers (PLCs), all integral to modern industrial operations.
The application of industrial electronic equipment spans various industries, including manufacturing, chemical processing, and robotics. These devices enhance productivity through automation and effective process control, enabling industries to meet growing demand while maintaining quality standards. As technology advances, the capabilities of industrial electronic systems continue to evolve, bringing new possibilities to industries worldwide.
Maintenance and troubleshooting of industrial equipment are vital for minimizing downtime and ensuring continuous productivity. Effective strategies include preventive maintenance and the use of software tools to identify common issues swiftly. As equipment ages, upgrading components can significantly improve performance and extend the life cycle of industrial systems.
Advancements in industrial electronic technology, such as Industry 4.0 and the Internet of Things (IoT), are revolutionizing the landscape of industrial equipment. These innovations not only enhance communication and data analytics but also improve energy efficiency and support advanced automation techniques, thereby changing how industries operate and compete today.
Investing in a durable industrial pc case can protect your components and enhance system longevity.
Types of Industrial Electronic Equipment
Control systems are at the heart of industrial electronic equipment, allowing for precise management of machinery and processes. They include hardware and software components that monitor inputs, process information, and generate outputs to automate operations. These systems can vary in complexity from basic relay controls to sophisticated distributed control systems (DCS).
A modern gsm modem streamlines communication in industrial settings, ensuring seamless connectivity and data transfer.
Sensors and actuators serve as critical components in industrial electronic equipment. Sensors detect physical variables such as temperature, pressure, and position, while actuators convert control signals into physical action, moving or controlling a system element. Together, they provide real-time feedback and operational control, enabling efficient process management.
Power supplies and distribution systems are essential for the reliable functioning of industrial electronic equipment. These systems provide the necessary electrical energy required to operate various devices and ensure that power is distributed safely and efficiently throughout the facility, safeguarding against overloads and faults.
For those working in demanding environments, a reliable dust proof keyboard is essential for maintaining productivity.
Programmable logic controllers (PLCs) are specialized computers widely used for automation and control of industrial processes. They are designed to withstand harsh industrial environments and offer a user-friendly programming interface, empowering engineers to develop automation solutions tailored to specific operational needs.
Applications of Industrial Electronic Equipment
Automation in manufacturing is one of the primary applications of industrial electronic equipment, facilitating continuous production with minimal human intervention. This technology allows for faster and more accurate operations, reducing labor costs and increasing overall output while maintaining high quality.
Monitoring and data acquisition systems are vital for tracking performance metrics and operational efficiencies. By utilizing industrial electronic equipment, organizations can gather real-time data, analyze production processes, and make informed decisions to optimize operations and reduce waste.
Process control in chemical industries heavily relies on industrial electronic equipment to manage chemical reactions and maintain safety standards. Precise monitoring and control of temperature, pressure, and flow rates ensure that chemical processes run smoothly and safely, minimizing risks associated with hazardous materials.
Robotics and mechanization in production are greatly enhanced by industrial electronic equipment. Robots equipped with sensors and control systems can perform complex tasks, from assembly to packing, with a level of precision unattainable by manual labor. This integration leads to a more efficient and adaptable production line.
Maintenance and Troubleshooting of Industrial Equipment
Preventive maintenance techniques are essential for sustaining the performance of industrial electronic equipment. Regular inspections, cleaning, and testing can identify potential problems before they escalate, allowing for timely intervention and prolonging the operational life of equipment.
Common issues with industrial electronic equipment include power failures, sensor malfunctions, and software glitches. Troubleshooting involves systematic diagnosis of these issues, often using observational techniques and diagnostic tools to determine the root cause and implement effective solutions.
Software tools for troubleshooting have become an invaluable asset in maintaining industrial equipment. These tools can identify patterns of failure, monitor conditions in real-time, and facilitate quick corrections, minimizing downtime and enhancing productivity.
Upgrading aging equipment is oftentimes necessary to improve functionality and efficiency. Outdated systems may hinder production capabilities and increase the risk of failure. By investing in modern technologies, companies can enhance their operational capabilities and adapt to evolving market demands.
Advancements in Industrial Electronic Technology
Industry 4.0 and the IoT have transformed industrial electronic equipment by enabling smarter processes and interconnected systems. This integration allows for real-time monitoring, predictive maintenance, and data analytics, creating an adaptive manufacturing environment that responds swiftly to changes in demand and resource availability.
Artificial intelligence applications in automation are pushing the boundaries of productivity and efficiency in industrial operations. AI algorithms can analyze vast amounts of data, enabling predictive maintenance, quality control, and decision-making processes, thus optimizing production workflows and reducing operational costs.
Energy efficiency improvements are a significant focus in industrial electronic technology. New equipment designs and automation strategies help minimize energy consumption and reduce environmental impacts, supporting companies in their sustainability initiatives while also lowering operational expenses.
Emerging trends in sensor technology are reshaping the landscape of industrial electronic equipment. Advanced sensor materials and designs are leading to increased sensitivity, accuracy, and miniaturization, creating more efficient systems that require less maintenance and are easier to integrate into existing infrastructures.
Safety Standards for Industrial Electronic Equipment
Regulatory requirements for equipment safety are critical in ensuring industrial electronic equipment operates safely and effectively. Compliance with local and international safety standards protects personnel, equipment, and the environment, highlighting the importance of adhering to these regulations.
Best practices for safe equipment operation include regular training for employees, implementing safety protocols, and ensuring proper maintenance of equipment. These practices create a safer work environment and minimize the risk of accidents or equipment failure that could disrupt operations.
Risk assessment in industrial environments is vital for identifying potential hazards associated with equipment operation. This process involves evaluating risks, hazards, and operational practices to implement necessary safety measures and ensure a safe working environment for all personnel.
Safety certifications and testing procedures provide assurance that industrial electronic equipment meets established safety standards. Manufacturers often seek certifications from recognized organizations to validate the safety and reliability of their products, instilling confidence in their use in industrial applications.